こんにちは、コロスケです。
今日は、電子部品の生産中止問題についてまとめていきます。
電子部品を購入している製造業の方にとって、電子部品の生産中止問題は深刻ですよね。
昨今電子部品の生産中止は増加傾向にあります。
中には、生産中止部品が手配後に発覚して、緊急で切り替え対応をした方もいるかと思います。
モノ作りを続けるにあたって、メーカーである我々は生産中止問題とどのように向き合っていくべきでしょうか。
今回は10年以上生産中止問題に取り組んできた僕が、電子部品の生産中止対策について詳しく解説していきます。
・生産中止部品が多くて困っている
・どうすれば生産中止対応の仕事が減らせるの?
上記、生産中止問題で苦労している方向けに有益な情報を提供致します。
電子部品の生産中止(ディスコン・EOL)対策を現役資材部員が解説
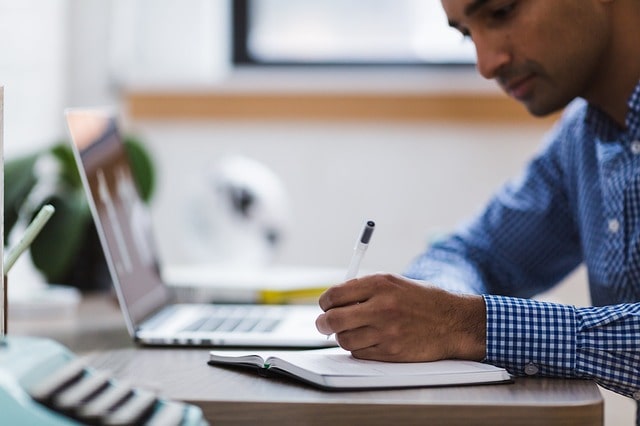
本記事の結論です。
・資材部門は年に一度、購入実績の品目全ての調査をするべき
・設計部門は安易な設計流用を見直すべき
・資材部門は常に市場のトレンドの把握に努めるべき
電子部品の生産中止問題への取り組みは、製造業の競争力向上にもつながる大事な活動です。
しかし、今の日本の製造業には、生産中止対応にお金をかける余裕がありませんし、経営者もお金にならないとの理由で本腰を入れて取り組むことをしません。
そういった厳しい状況で、どのように生産中止問題に取り組めばよいのかを一つずつ解説していきます。
電子部品に生産中止が多い理由
機器や素材と比べて、電子部品は生産中止となりやすい品目です。その理由は以下の3つです。
製品のライフサイクルが短い
電子部品は他の材料と比べて、製品のライフサイクルが非常に短いです。
例えば抵抗・コンデンサは、市場の小型化のニーズに対応して、どんどん製品が小型化してきています。
他にも市場の技術ニーズに合わせて、数年スパンで新製品がリリースされる特徴があります。
生産の効率化
新商品が頻繁にリリースされると、取引先の生産品目がどんどん増えていきます。
リリースから一定期間経ち、需要も減少している古い製品は、メーカーにとって製造するメリットは少ないです。
そのため、あまり売れていない製品は、生産効率を上げるために一定のタイミングで生産中止にしていきます。
生産中止による、生産効率化を大々的に進めているのが村田製作所のMLCCです。
現在村田製作所は、生産効率の悪い1608サイズのMLCCを生産中止にすることを発表しています。
サプライヤーの体力低下
昔は、客先との付き合いなどで、採算が取れない品目であっても、継続して製造してくれるケースがありました。
しかし、昨今は経営状況に余裕の無いメーカーが多いので、足手まといの製品を作り続ける余裕が無くなってきています。
その結果、利益が取れないラインナップを一気に生産中止にすることも増えてきています。
こういった動きは、サプライヤーの選択と集中と呼ばれており、サプライヤーにとってはメリットが多いです。
一方で購入側である我々にとっては、切り替え手続きが必要になるなどメリットは、ほとんどありません。
電子部品の生産中止での課題
以前はあまり注目されることが無かった生産中止対応ですが、最近は要約製造業の需要な課題として認識されつつあります。
生産中止対応での具体的な課題を3つご紹介致します。
問題1:急な生産中止対応の負荷
生産中止対応での一番の問題点が「急に生産中止部品が発覚する」ことです。
久しぶりに手配した部品が、手配後に生産中止であることが発覚、緊急で部品の切り替えが必要になるケースがあります。
直前で生産中止が発覚すると、社内の生産がストップしたり、余計な設計工数・会議の時間が発生したりします。
兎にも角にも急な生産中止対応は、社内の関係者全員を疲弊させてしまうので、早急な改善が必要となります。
問題2:生産中止品の切り替えは1円にもならないことが多い
生産中止対応が重要であることは皆認識しています。
しかし、現状経営者・管理層は抜本的な対策をなかなか取りません。その理由は何故でしょうか。
一番の理由が「生産中止対応はお金を生み出さないから」です。
要は付加価値が低いんです。
生産中止の対応は必要な作業ですが、それ自体では1円にもならないことが多いです(部品切り替えで価格が下がらないケースも多いです)。
そのため、経営層・管理層は、付加価値が低いと判断し、リソースを別の所へ配分してしまいます。
その結果、苦労するのは我々現場です。
頑張っても製造原価が下がる訳でも無いので、評価されにくいですし、仕事ばかり増える結果になります。
問題3:ラストバイによる在庫の増加
3つ目の課題が、ラストバイを実施することによる在庫の増加です。
生産中止部品が発生した時は、一定期間分の必要数をラストバイします。
ラストバイを行う時は、安全係数をかけて手配したり、手配後に見込みが変わるなど、在庫が長期に渡り滞留するケースがあります。
最悪なケースでは、デッドストックとして使用されないまま廃却されることもあり得ます。
棚残の増加は経営上マイナスです。
ラストバイで在庫が増えることで、会社の経営体力も奪われていきます。
生産中止対応で疲弊しないための具体的な対策3選【電子部品】
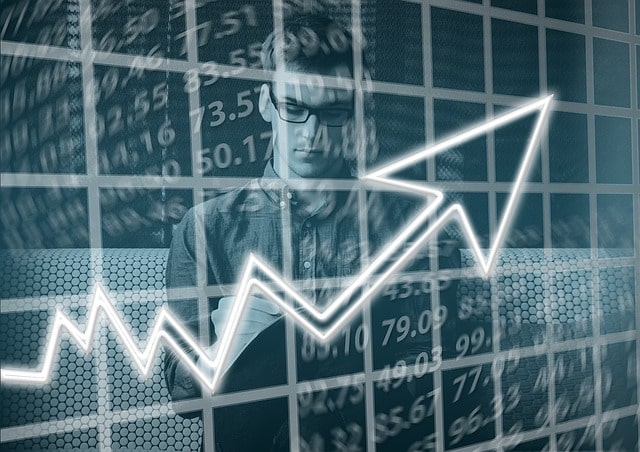
先ほどご説明したように、生産中止対応は色々な問題を抱えています。
これらの課題を解決するための具体的な対策を3つご紹介していきます。
対策1:定期的に購入実績品全ての調査を行う
当たり前の対策なのですが、これをきちっと出来ていれば、直前で生産中止であることが判明するリスクを避けることが出来ます。
具体的な調査手順は以下の通りです。
定期的に調査を行い、隠れた生産中止部品を特定する
個人的には一年に一度は部品リストの生産状況確認を行うべきと考えています。
定期的な発注がかからない部品は、メーカーの生産中止連絡が漏れている可能性があります。
また資材担当者側での不備で展開が漏れている可能性もゼロではありません。
こういった隠れた生産中止部品を見つけるために、一年に一度は棚卸をすることをおすすめしています。
基本は登録部品全てを調査すべき
生産状況調査では、直近1年の実績など、範囲を限るケースが一般的です。
しかし、僕は基本的には期間を絞らず実績品は全て調査すべきと考えています。
その理由は、たまに発注がかかる部品が調査から漏れるからです。
問題が発生するのは、たまにしか発注しない部品です。
ここをカバーできないと結局直前で問題が発覚することになります。
確かに、件数が多いと調査する資材部門も、回答する取引先も非常に手間がかかります。
しかし一度、生産中止の問題が発生すると、緊急の対応に多くの時間が割かれます。
将来発生する可能性がある工数を考えると、僕は時間をかけてでも調査する価値はあると考えています。
担当者に依存しない仕組みの構築する
電子部品の生産中止は、サプライヤーの営業から通知があり、これを資材部門が受領、社内関係者へ展開するケースが一般的です。
しかし、担当者の力量不足や怠慢、その他色々な理由で、社内へ展開されないケースがごくまれに発生します。
これは資材部門の構造的な課題と言えるかもしれませんが、管理職は担当者の力量に依存しない仕組みを構築することで、もれなく生産中止情報を所内に展開していく必要があります。
対策2:安易な設計流用は止める
生産中止対策では、安易な設計流用を止めることが非常に重要になります。
設計流用は、設計工数を削減する有益な方法です。
しかし、設計の流用によって生産中止リスクが高い部品がそのまま採用されることにつながります。
確かに、従来は費用対効果で設計流用の方がメリットが大きかったかもしれません。
しかし、昨今の生産中止件数が多い状況では、きちんと設計で部品の見直しを図る方が、トータルではメリットがある状況に変わってきています。
設計部門の方は、新規設計時は基板に搭載される電子部品の生産状況をきちんと確認していくことが重要です。
対策3:市場トレンドの把握・共有
対策の3つ目は、資材調達部門が市場トレンドをきちんと把握することです。
メーカーの開発がどういう方向に進むのか、今採用している部品が今後も継続的に供給されるのか、これらロードマップを資材部門が入手することが重要です。
取引先との面談の重要性
情報を入手するのに一番良い方法が取引先との面談です。
取引先と面談するのは時間が取られるので嫌がる資材部員も居ますが、それは間違いです。
取引先から有益な情報を仕入れることが出来れば、面談は非常に生産性の高い活動と言えます。
もちろん毎週面談する必要はありませんが、定期的に打合せを行い、製品ロードマップを入手することは資材の付加価値に繋がります。
資材部門は、取引先から積極的に情報を入手するようにしましょう。
市場トレンドを設計部門と共有する
そして取引先から得た情報は惜しみなく設計部門へ展開しましょう。
せっかく得た情報でも設計者が把握していないと、何の意味も成しません。
設計部門が今後のトレンドを把握することで、新規部品検討時に相対的に生産中止リスクが低い部品を選定できるようになります。
まとめ
本記事のまとめです。
・資材部門は年に一度、購入実績の品目全ての調査をするべき
・設計部門は安易な設計流用を見直すべき
・資材部門は常に市場のトレンドの把握に努めるべき
生産中止対応の負荷は年々高まっています。
昨今は村田のMLCCやルネサスなど多くの生産中止が発生しております。
今後もメーカーの選択と集中の流れは継続していきます。
従来の運用では我々現場の人間は疲弊してしまいます。
現場の生産性を高めるためにも上記の対策を実施していくことで、生産中止対応の在り方を見直していくことが非常に重要です。
そして資材部門はその分野で大きな貢献をすることが出来ます。
資材部門の人は、生産中止問題を避けるべきものと考えるのではなく、資材の存在価値を高めることが出来る絶好のチャンスと考えて頑張っていきましょう。
最後まで読んでくれてありがとうございました。
このブログ( Corosuke blog)では、僕が働く「資材・購買業務の紹介」や「日々の生産性向上による生活の質UP」「投資を通じた自己実現」などをまとめています。
良かったら、他の記事も読んでみて下さい。きっとあなたの役に立つ情報があると思います。
コメント